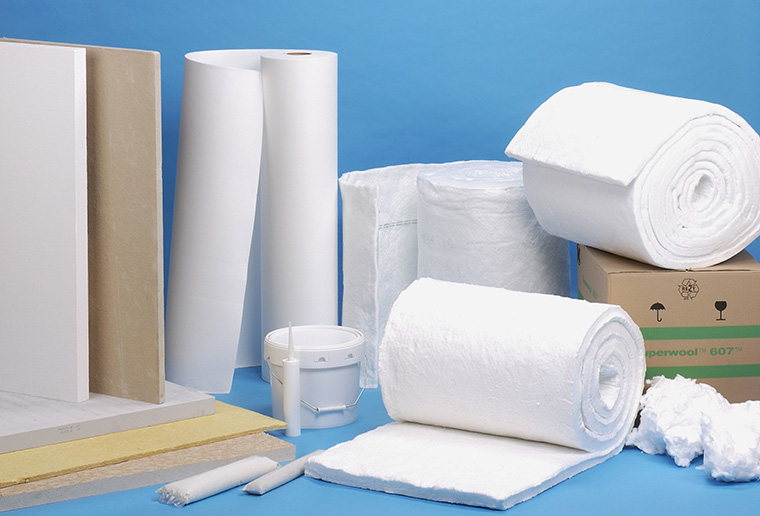
Refractory Materials
This range of refractory insulating products includes products made of wires either in biosoluble or ceramic fibres. Blankets are used to build insulating refractory linings in industrial furnaces. Felts are used as expansion joints. The boards are more suitable to boiler linings, or for back up insulation. Mastics are used to fill up the cracks and injected insulation.
Refractory materials generally refer to the inorganic nonmetal materials with a refractory degree of 15800C or above. Refractory materials include natural ores and various products made by certain purposes and requirements through certain processes, which have certain high-temperature mechanical properties and good volume stability. They are the necessary materials for various high-temperature equipment.
Ceramic Fiber Linings (sequence D) Material Types
- 26 Insulating Refractory Fibrouse Products
- 27 Insulating Refractory Bricks
- 28 Braids, Ropes, Textiles In High T Fibres
- 29 Metallic Fibres For Refractory Castables
Insulating Refractory Fibrouse Products
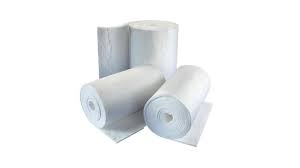
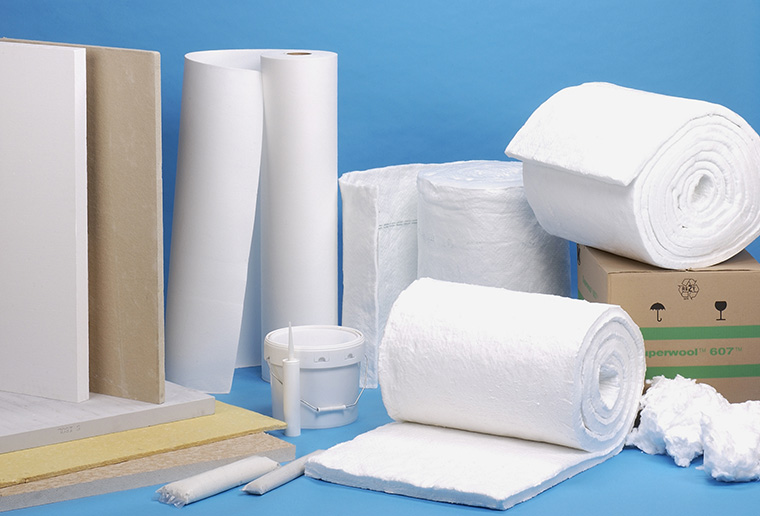
This range of refractory insulating products includes products made of wires either in biosoluble or ceramic fibres. Blankets are used to build insulating refractory linings in industrial furnaces. Felts are used as expansion joints. The boards are more suitable to boiler linings, or for back up insulation. Mastics are used to fill up the cracks and injected insulation.
Insulating Refractory Bricks
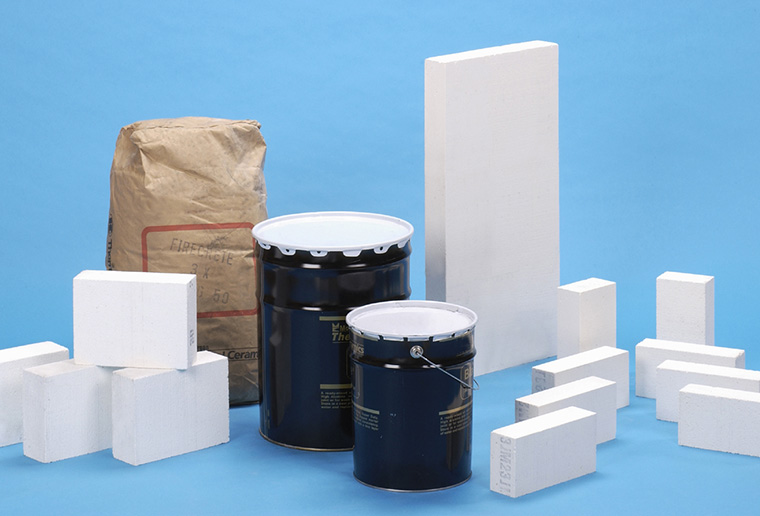
Used in the furnace linings, these insulating refractory bricks induce significant energy savings due to their excellent insulating properties combined with their physical properties. They are particularly recommended to be used in reducing atmosphere.
The range includes six qualities which respectively brand named : JM23, JM26, JM28, JM30, JM32, JM34.
Apart from these bricks, there is a large range of castables which offer similar advantages, as well as insulating refractory cements which are used for gap filling.
Braids, Ropes, Textiles In High T Fibres
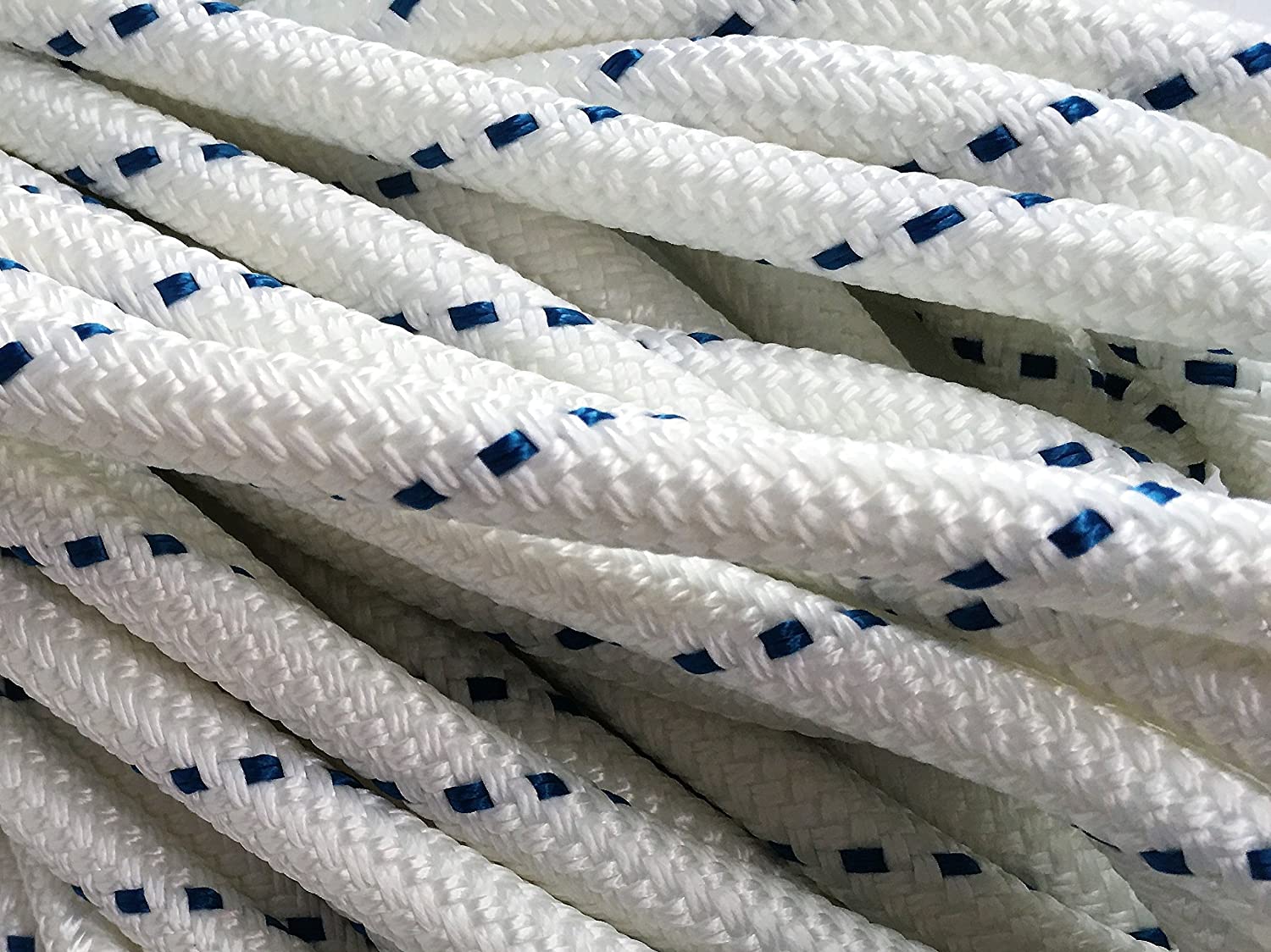
Natural and synthetic fibre ropes have been discussed in tenns of their properties, behavioural characteristics and applications. A comparative assessment of the attributes of the fibres used in ropes has also been made.
braiding, in textiles, machine or hand method of interlacing three or more yarns or bias-cut cloth strips in such a way that they cross one another and are laid together in diagonal formation, forming a narrow strip of flat or tubular fabric. The word plaiting is generally applied when such materials as rope or straw are employed.
Rope has been in use for a long time and has played an useful role In the progress of civilization. It has an unique property of resisting large axial load in comparison to bending and torsional load. A variety of natural fibres has been used as a basic element in rope construction for centuries. Today, with the advent of synthetic fibres, the field of application has widened with associated improvement in performance. With the progress in manufacturing technology, newer constructions are being made with improved performance. As a result, a variety of rope now finds its way in household, industrial, civil construction and defence sectors for performing a varIety of task. Textile fibre rope has advantages over its metallic counterpart for a number of reasons (Table 1) and it is increasingly being preferred in many applications over metallic ropes.
Metallic Fibres For Refractory Castables
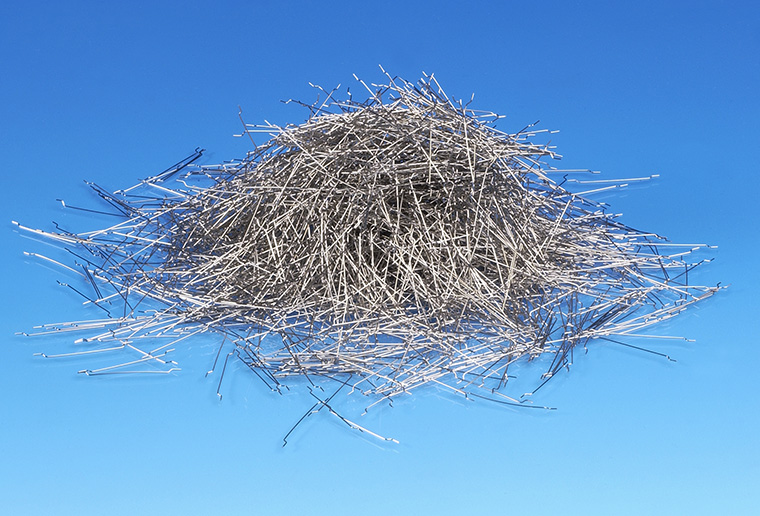
Used as an addition to the castable mixing to improve its thermal shocks and its mechanical shocks resistance, the metallic fibres look like micro armatures. Because they control the cracks development, these micro armatures improve cohesion and strength of the refractory castable.
The DL fibre, made out by wiredrawing with a hook at each extremity, is the best technical solution for severe applications. More economical, the straight fibre ML, is suitable for less severe applications.
More economical, the straight fibre ML, is suitable for less severe applications.
Alliages : aisi 304, aisi 310, aisi 446, aisi 430
The best technical solution for severe applications.
Alliages : aisi 304, aisi 310, Low carbon (LC)